Metallografia dei componenti microelettronici
La maggior parte dei componenti microelettronici è prodotta in serie, quindi, il controllo qualità si limita a test di ciclaggio termico per individuare i pezzi difettosi. Tuttavia, la metallografia svolge un ruolo importante:
- Sviluppare, progettare e condurre l'analisi dei guasti di componenti dei circuiti integrati: Le sezioni trasversali dei componenti vengono esaminate per identificare potenziali microvie, cricche, vuoti, sfere di saldatura, strati conduttivi o collegamenti
- Controlli a campione: Vengono condotti in diverse fasi della produzione
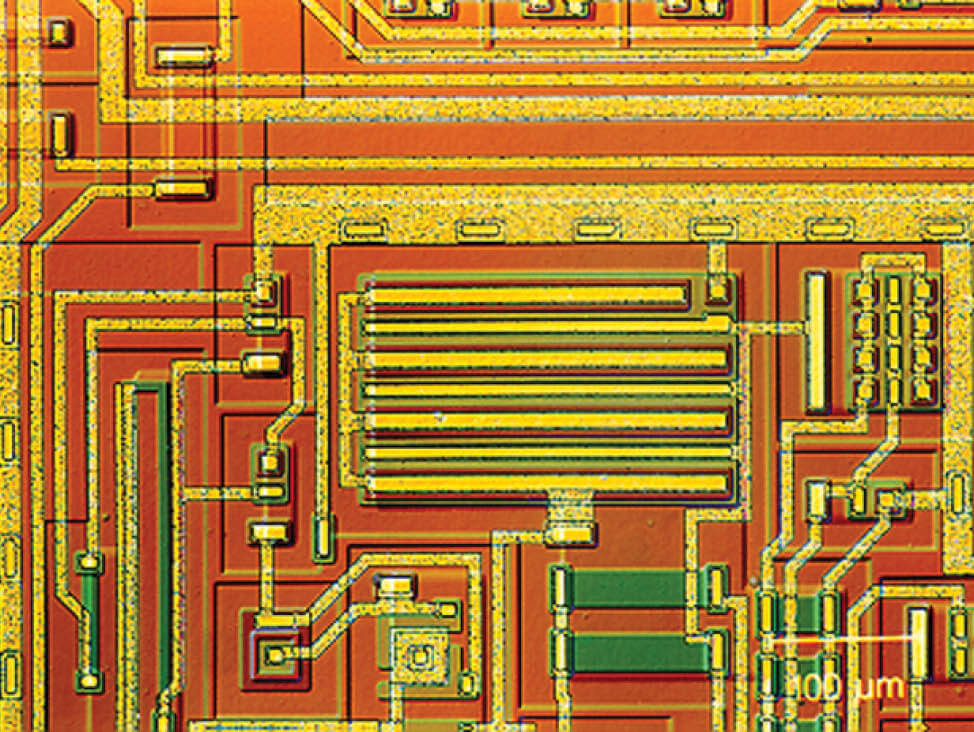
Fig. 1: Dettaglio di un circuito integrato lineare con fili conduttivi, resistenze, microvie e condensatori al centro

Fig. 2: Sezione trasversale di un wafer di silicio con fili conduttori di un circuito integrato

Fig. 3: Componenti inglobati su un circuito stampato
I componenti microelettronici contengono materiali diversi, come vetro, ceramica, metalli e polimeri, con proprietà molto diverse. La preparazione dei campioni richiede quindi una rimozione del materiale controllata, che permetta di rivelare le singole caratteristiche di questi materiali.
I controlli generalmente includono:
- Dimensione e distribuzione dei difetti: come vuoti, inclusioni e cricche
- Incollaggio e adesione dei materiali e delle loro interfacce
- Dimensioni e forma dei diversi componenti dell'assieme: spessore dello strato, fili, menischi di saldatura
- Porosità e cricche nella ceramica
- Planarità e ritenzione dei bordi (vengono ispezionati ad alto ingrandimento strati molto sottili tra i materiali)
A causa delle loro dimensioni e complessità, i componenti microelettronici possono essere estremamente difficili da preparare per l'analisi metallografica. Pertanto sono necessarie tecniche e apparecchiature di preparazione speciali per garantire un'adeguata precisione durante la rimozione materiale controllata.
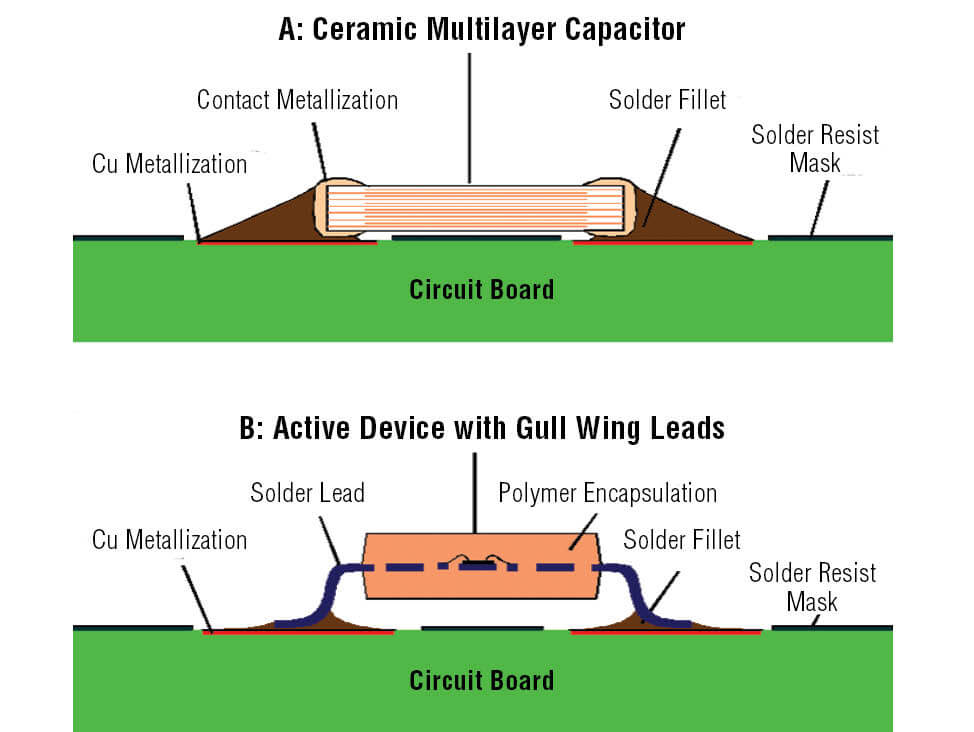
Fig. 4: Esempio di composizioni di materiali in componenti microelettronici
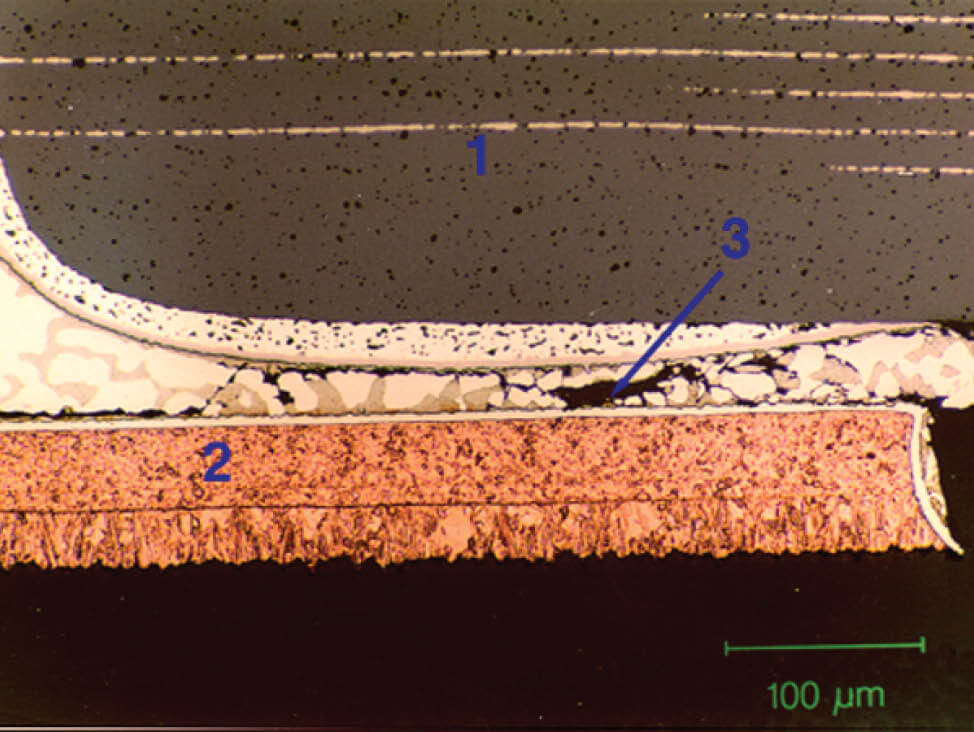
Fig. 5: Condensatore multistrato (1) saldato su una metallizzazione in rame del circuito stampato (2); cricca da fatica (3) che si propaga in continuazione attraverso la saldatura


Fig. 6 a & b: Ceramica e rame che mostrano differenze di planarità ad alto ingrandimento: a) prelevigatura iniziale fine con foglio/carta di carburo di silicio; b) prima prelevigatura diamantata fine su MD-Largo, disco di prelevigatura fine